Microfluidic Chemical Plant Project
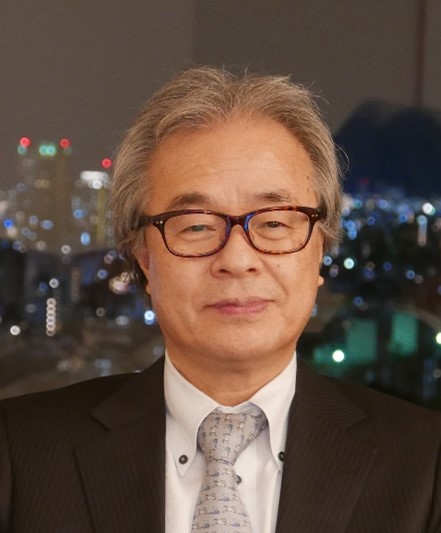
Microfluidic Chemical Plant Project aims to miniaturize huge chemical plants by arranging numerous small glass chips (microfluidic devices). Based on the research results accumulated by the University of Tokyo/KAST Kitamori Group, chemical reactions and processes are precisely controlled to produce high-performance chemical products. We will also contribute to the realization of a sustainable society by producing only what is needed, when it is needed, and in the amount needed using the compact, efficient, and smart chemical plants for the next generation.
Project Leader
Takehiko Kitamori
Research Period
Microfluidic Chemical Plant Project April 2023 ~
Research Location
AIRBIC A40 7-7, Shin-Kawasaki, Saiwai-ku, Kawasaki-shi, Kanagawa 212-0032 JAPAN
Research Outline
Microfluidics, a technology that allows liquids to flow in channels as thin as a hair (several hundred micrometers), is drawing attention in the fields of chemistry and biotechnology. Unlike traditional flasks and test tubes, solutions in microfluidic channels mix instantly in a small space and maintain a homogeneous temperature. This enables precise control of chemical reactions. Additionally, the efficiency of chemical reactions on the surfaces of electrodes and catalysts is enhanced due to the small, confined spaces of the microchannels. Thus, microspaces provide ideal environments for chemical reactions. However, to produce chemicals in large quantities, thousands of microchannels must be integrated. Moreover, to ensure homogeneous conditions in the liquid flows and chemical reactions across all microchannels, numerous pumps and sensors are required, matching the number of microchannels. This project aims to develop the world’s first desktop chemical plant featuring a large array of microfluidic devices, leveraging experiences from the Kitamori Project (1998-2003) and the Microchemistry Group (2003-2009) of KAST (the predecessor of KISTEC). In collaboration with Daicel Corp. and National Tsing Hua University in Taiwan, we will achieve large-scale parallelization of microfluidic devices. If we can successfully downsize a huge chemical plant using these devices, we will create space-saving, energy-efficient chemical plants for the future. Such plants will contribute significantly to reducing carbon dioxide emissions and other environmental impacts.
Content of research
1. Microfluidics for Integrated Chemical Processes
An example of metal ion analysis integrated into a microfluidic device is shown in Figure 1. Even in seemingly complex chemical processes, each operation is simple, such as mixing solutions or contacting or separating water and oil. These operations, which cannot be further simplified, are called unit operations. The core technologies of this project are to replace these unit operations with microfluidic devices (micro unit operations) and to reproduce the original chemical process by connecting them in series (continuous flow chemical process). To date, the project has been successful in blood analysis, ammonia monitoring in semiconductor manufacturing, and cancer drug production. In particular, the miniaturized immunoanalyzer successfully saved the life of a patient with a severe skin disease at The University of Tokyo Hospital.
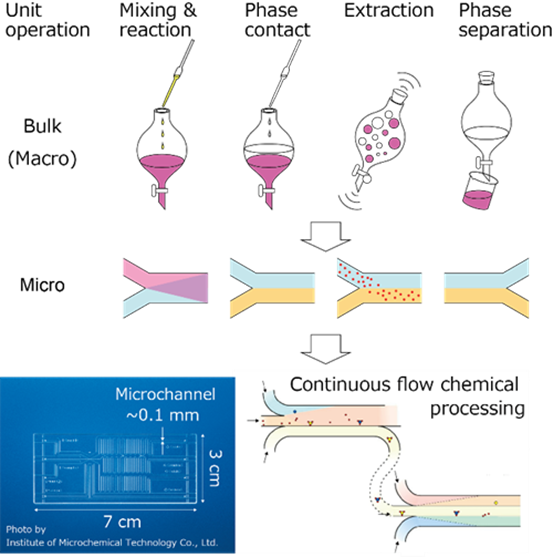
and Microfluidic Device
2. Spatio-Temporal Uniformity in Microspace
When adding milk to coffee, it’s necessary to stir them with a spoon. This is because when two solutions make contact, mixing occurs primarily due to the diffusion of solute molecules. However, diffusion alone is often insufficient for complete mixing, especially when the size of the container is significantly larger than the distance molecules can travel by diffusion. In microfluidic channels, on the other hand, the width and depth of the channel are comparable to the scale of molecular diffusion. Consequently, the concentration within the microchannel quickly becomes uniform due solely to diffusion. A similar principle applies to thermal diffusion. It is also well known that fluids in microfluidic channels exhibit laminar flow, meaning they flow in straight lines without turbulence. We refer to these characteristics—where the concentration, temperature, and flow velocity are consistently uniform throughout the microfluidic channels—as spatio-temporal uniformity. This uniformity is one of the greatest advantages for precisely controlling chemical reactions in microfluidic environments.
3. Serial-Parallel Large-Scale Integration of Microfluidic Devices
The primary challenge in this project is the massive parallelization of microfluidic devices connected in series. The University of Tokyo/KAST Kitamori group has already developed a particle manufacturing system that parallelizes 3,000 microfluidic devices. However, large-scale parallelization of serially-connected microfluidic devices remains unprecedented worldwide. Moreover, developing a new methodology for controlling extremely complex fluid circuits is imperative. To address these challenges, we plan to develop fluidic components, control systems, and computational simulations for reactive fluids in collaboration with the Department of Mechanical Engineering at National Tsing Hua University and a start-up company, IMT Taiwan. Additionally, we are actively engaging with small and medium-sized enterprises both within and outside Kanagawa that possess advanced technological capabilities to jointly develop pumps, sensors, precision components, and other products. In partnership with Daicel Corp., we will demonstrate the pilot production of high-functionality chemical products using a prototype desktop chemical plant. This initiative is a significant step toward the social implementation of microfluidics.
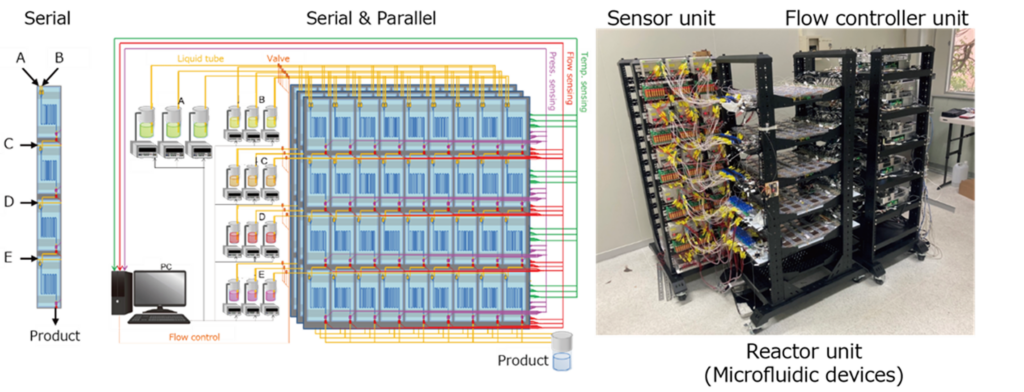